Die Überführung eines innovativen Verfahrens zur Schubprüfung an Faserverbundwerkstoffen in die anwendungsorientierte Praxis, optische Freiformflächen zur Entwicklung moderner optischer Geräte und Tools zur hybriden Wertschöpfung als Problemlöser erhalten DIN Innovationspreis.
Innovation hängt eng mit erfolgreichem Wissenstransfer zusammen. Drei Beispiele, wie Normen und Standards neues Wissen praktisch handhabbar machen, hat DIN am 8. April auf der Hannover Messe mit Innovationspreisen ausgezeichnet.
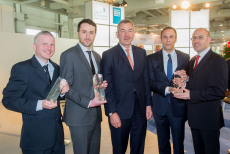
DIN-Innovationspreise: Die Gewinner auf der Hannover Messe (Bild:DIN)
In einer an der Universität Hamburg vorgelegten Master-Arbeit ist Gerald Däuble der Frage nachgegangen, welche Determinanten den Erfolg hybrider Produkte und somit die hybride Wertschöpfung beeinflussen. Bei der hybriden Wertschöpfung, d. h. der Bündelung von aufeinander abgestimmten Produkten und Dienstleistungen, stehen nicht feste Einheiten von Sach- und Dienstleistungen im Blickpunkt, sondern die Problemlösung für den Kunden. Sie wird als Strategie der Kundenbindung immer häufiger auch von kleinen und mittleren Unternehmen eingesetzt. Bisher fehlte hierfür eine integrierte Betrachtung der Wirkungszusammenhänge verschiedener Determinanten über den gesamten Lebenszyklus. Diese sind als Entscheidungsgrundlage für ein erfolgreiches Management hybrider Leistungsbündel unabdingbar. Kernziel der Arbeit von Däuble war es daher, ein Modell zur Entscheidungsunterstützung im Bereich der hybriden Wertschöpfung zu erarbeiten. Das vom BMWi geförderte Projekt „Leitlinien für die Bewertung von Lebenszykluskosten in Produkt-Dienstleistungssystemen“ im Rahmen des INS-Förderprogramms ermöglichte es dem Autor, auf umfangreiches Expertenwissen aus der Praxis zuzugreifen. Die für die praktische Anwendung relevanten Ergebnisse dieser Arbeit wurden in die DIN SPEC 77234 überführt.
In seinem prämierten Beitrag hat Dirk Jahn, Optikdesigner bei der Carl Zeiss AG in Jena, das Thema optische Freiformflächen behandelt. Für die Entwicklung moderner optischer Geräte sind komplexe Freiformflächen zwingend notwendig. So lässt sich z. B. durch Verwendung von Freiformflächen für eine reflexfreie Funduskamera, die in der Augendiagnostik zum Einsatz kommt, ein Projektionssystem mit einem ultimativen Kontrast von 2500000:1 herstellen. Bei der Verwendung von Freiformflächen stößt man allerdings in der kompletten Fertigungskette auf bisher unbekannte Probleme. Beispielsweise bei der Datenübertragung vom Optikdesign zur Konstruktion oder Fertigung sind Datenformate und Konventionen oft fehleranfällig oder unzureichend. Darüber hinaus weisen die gefertigten Teile Fehler auf, die sich nicht mehr mit den üblichen Mitteln beschreiben lassen. Solche Probleme werden in der herkömmliche Entwicklung und Fertigung durch Nutzung von Symmetrien und durch Anwendung passender Normen vermieden. So lag es nahe, zur Unterstützung dieser neuen Flächenformen ein einheitliches Vorgehen in Form einer Norm festzulegen. In seinem Beitrag zeichnet Jahn den Weg von einem nationalen, vom BMWi geförderten Projekt zur Entwicklung einer Internationalen Norm, ISO 10110-19, die jetzt als Entwurf vorliegt.
Der dritte DIN-Innovationspreis ging an die Jungunternehmer Dr.-Ing. Fabian Grasse und Malte Zur für die Überführung ihres innovativen Verfahrens zur Schubprüfung an Faserverbundwerkstoffen in die anwendungsorientierte Praxis. Auch hier wurde bei DIN eine Spezifikation erarbeitet: DIN SPEC 4885. Die bisherigen Prüfverfahren für Faserverbundwerkstoffe sind häufig für die besonderen Anforderungen der neuen Werkstoffe nur bedingt geeignet. Das gilt insbesondere für die Bestimmung der Schubeigenschaften. Ehe sie ihre eigene Firma in Berlin gründeten, arbeiteten beide bei der Bundesanstalt für Materialforschung und Prüfung (BAM),wo sie mit der Prüfung und Simulation von Faserverbundwerkstoffen in engere Berührung kamen, und ihnen deren großes Zukunftspotential bewusst wurde. Dort waren sie auch an der Entwicklung eines ersten Prototyps des Schubrahmens beteiligt. Hierbei wurde ihnen klar, dass es für einen solchen Schubrahmen durchaus Nachfrage aus der Industrie gab, aber dass diese eine bessere Kennwertermittlung von Faserverbundwerkstoffen erwartete. Das setzte aber eine substantielle Weiterentwicklung des Schubrahmens voraus, da insbesondere die Prüfdauer und der Probenwechsel noch ungelöste Probleme darstellten. Dieser Probleme haben sich die Ingenieure dann in ihrer eigenen Startup-Firma Grasse Zur Industriegesellschaft mbH angenommen und gelöst. Das Verfahren haben sie zu einem Schubprüfsystem weiterentwickelt und für den industriellen Einsatz optimiert. Mit der Dokumentation des Verfahrens in einer DIN SPEC sollen die Bekanntheit und Akzeptanz des Verfahrens noch gesteigert werden.