Werkstoffe mit Selbstheilungskräften made in Freiberg
Sie forschen an den Hochleistungsmaterialien von morgen: An Werkstoffen mit Gedächtnis und an Materialien, die Risse selbst schließen können.
Die Wissenschaftler um Dr. Thomas Niendorf haben nun eine Anlage erhalten, die das Herzstück des Projekts bildet. Der 3D-Drucker für Metalle schafft neue Werkstoffe, deren innerer Aufbau ihnen faszinierende „Selbstheilungskräfte“ verleiht.
Die Anforderungen an moderne Werkstoffe und Herstellungsprozesse sind hoch: Gerade in der Automobil- und Luftfahrtindustrie sind Leichtbauteile gefragt, die fest, widerstandfähig und kostengünstig sind. „Vor diesem Hintergrund wollen wir sogenannte Smart Materials herstellen, also Werkstoffe mit eingebauter Intelligenz“, erklärt Dr. Thomas Niendorf, Leiter der Forschergruppe. „Die neuen Werkstoffe können dann beispielsweise einen Riss im Material selbstständig schließen oder nach Verformungen ihre Ausgangsform wieder einnehmen.“
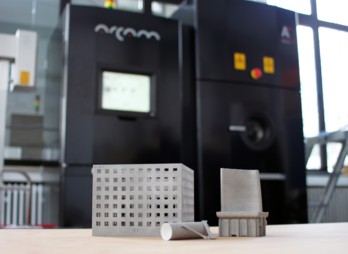
Kernstück des Forschungsprojekts ist eine Anlage zur additiven Fertigung, im Volks-mund: Ein 3D-Drucker für Metalle. Dieses neue Großgerät ist nun eingetroffen, die ersten Versuche laufen bereits.
Für die Anwendung muss das gewünschte Bauteil zunächst im Computer konstruiert, und dann in Schichten zerlegt werden. Die Informationen zu den einzelnen Schichten werden dann an die Anlage gesendet, die in einem ersten Schritt loses Pulver in der gewünschten Menge aufträgt und anschließend entsprechend den Konturen des Bauteils in der jeweiligen Schicht das Pulver mittels eines Elektronenstrahls verschmilzt. Dieses Prozedere wird Schicht für Schicht wiederholt, bis das Bauteil fertig ist. „So entsteht ein Werkstoff, der sich mit gegossenen und geschmiedeten Strukturen messen lassen kann“, betont Dr. Thomas Niendorf.
Durch dieses „Electron Beam Melting“-Verfahren erhalten die Werkstoffe eine spezielle Mikrostruktur und können erstmals mehrere spezielle Materialeigenschaften in sich vereinen. Sogenannte Formgedächtniswerkstoffe etwa lassen sich verformen und nehmen nach einer Erwärmung ihre ursprüngliche Form wieder an. „Ein viel zitiertes Beispiel ist die Büroklammer. Wenn ich die verforme und anschließend in ein heißes Wasserbad lege, springt die Büroklammer wie von Geisterhand wieder in ihre alte Form zurück. Das kann ich später auf beliebige Strukturen übertragen“, veranschaulicht Dr. Thomas Niendorf die Funktionsweise.
Bislang werden nur wenige Metalle nach diesem Prinzip verarbeitet. Interessant könnten die im Projekt erforschten neuen Materialien etwa für den Automobilbau oder für die Luftfahrt sein. Dort ist es zum Beispiel wichtig, die Flügelstrukturen an die jeweilige Flugsituation anzupassen. Momentan übernehmen das hydraulische Antriebssysteme, die entsprechend viel Platz und komplexe Leitungssysteme benötigen. Mit dem neuen Verfahren ist es denkbar, die Flügel von Flugzeugen nur durch Erwärmen oder Abkühlen optimal anzupassen. So ließe sich effektiv Platz und Gewicht bei der Konstruktion von Flugzeugen einsparen.
Das Forschungsprojekt wird im Rahmen des Emmy Noether-Programms der Deutschen Forschungsgemeinschaft für fünf Jahre mit rund zwei Millionen Euro gefördert. Dr. Thomas Niendorf hat in Paderborn studiert und promoviert. Mit seiner Forschergruppe ist er bewusst an die TU Bergakademie Freiberg gekommen. „In Freiberg steht mir die gesamte Prozesskette zur Verfügung, die ich für dieses Projekt brauche. Von der Stahlherstellung über jede Form von Verarbeitung bis hin zu Charakterisierung und Ermüdung dieser hergestellten Strukturen – alle wichtigen Projektstationen sind innerhalb von 500 Metern erreichbar. So kurze Wege kann kein anderer deutscher Standort bieten.“