Nachhaltigkeit in Unternehmenskonzepten „The Green Machine“
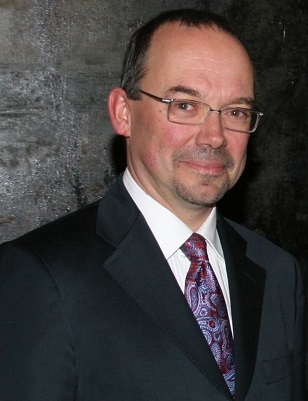
Trägt einen großen Namen: Peter D. Dornier, Chef der Lindauer Dornier GmbH Enkel des legendären Flugzeugkonstrukteur Claude Dornier
„Gewebe als in sich digitale Strukturen haben ein spannendes Potenzial“
Peter D. Dornier, Geschäftsführungsvorsitzender der Lindauer DORNIER GmbH, über den Aufbruch in „neue textile Welten“
Das Weben als eines der ältesten Fertigungsverfahren der Menschheit steht im Zeitalter technischer Textilien vor neuen, spannenden Entwicklungen, sagt Peter D. Dornier, Geschäftsführer und Mitinhaber der Lindauer DORNIER GmbH. Sein im VDMA engagiertes Unternehmen ist Weltmarkt- und Technologieführer im Bau von Webmaschinen. 60 Prozent aller Carbon- und Aramidgewebe, 50 Prozent aller Glasfasergewebe und zwei von drei Airbag-Kissen sowie drei von vier Autoreifen weltweit werden auf Maschinen vom Bodensee gewebt.
Pioniergeist und der Name Dornier bedingen sich seit fast einem Jahrhundert…
… wie ein roter Faden in unserer Unternehmensgeschichte: Den „Dornier Spirit“, das stetige Streben nach technischem Fortschritt, hat mein Großvater und Flugzeugkonstrukteur Claude Dornier schon als Mitarbeiter von Graf Zeppelin geprägt; das wurde meinem Vater, der Firmengründer der Lindauer DORNIER GmbH, weitervererbt und ist bis heute eines unserer Markenzeichen. Unsere Maxime bei allen Entwicklungen war und ist deshalb: Mit der besten Technologie den maximalen Kundennutzen anbieten.
Um einige Meilensteine aus jüngster Zeit zu nennen: Ganz aktuell ist das Label „DORNIER Composite Systems®“, unter dem wir unsere Kompetenzen im Bau von Webmaschinen und Folienreckanlagen für einen effizienteren Fertigungsprozess von Hochleistungsverbundwerkstoffen aus Folie und Fasern bündeln. Oder unser „The Green Machine“-Konzept mit dem Doppelaspekt, besonders leistungsfähige, gewebte Produkte für den Schutz von Mensch und Umwelt möglichst ressourcenschonend herzustellen. Diese Nachhaltigkeit gehört bei der Lindauer DORNIER GmbH seit der Gründung zur unternehmerischen DNA und das nicht nur weil unsere Webmaschinen nun schon 50 Jahre die gleiche, grüne Farbe tragen.
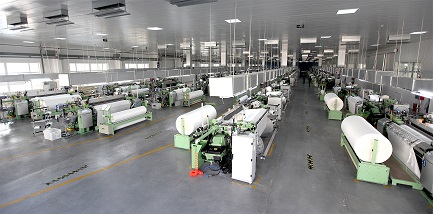
Wartungsarm, effizient, langlebig: DORNIER Greiferwebmaschinen-Anlage zur Herstellung von Präzisionsfiltergewebe zur Nass-, Feststoff und Luftfiltration
Wird Nachhaltigkeit auch auf der ITMA im November in Mailand eine Rolle spielen?
Ja. Zum Thema „The Green Machine“ beispielsweise werden wir eine Technik zeigen, die das bisher von uns technologisch Bekannte übertrifft. Für den Bereich Umwelt- und Personenschutz sind unsere grünen Webmaschinen zwar heute bereits der „Benchmark“, aber wir möchten die Anwendungsbreite noch erheblich erweitern. Ich denke dabei z.B. an einen Markt wie China, der für uns heute ein Viertel des Umsatzes ausmacht. Mit DORNIER Maschinen werden dort u. a. Filtergewebe zur – dringend erforderlichen – Reinhaltung von Wasser und Luft hergestellt. Unser „grünes“ Maschinenkonzept fußt übrigens auf der Grundidee der VDMA-Initiative Blue Competence, Maschinen oder Prozesse in Bezug auf den elektrische Energie- und Luftverbrauch bei steigender Leistung zu optimieren.
DORNIER geht bei der Nachhaltigkeit aber noch einen Schritt weiter, denn unsere Webmaschinen und Folienreckanlagen haben in der Regel eine 30- bis 40-jährige Nutzungsdauer, sind also mitnichten „Wegwerfprodukte“. Diese Anlagen, solange für die Kunden wirtschaftlich sinnvoll, zuverlässig, mit Ersatzteilen und Service zu unterstützen, ist eine unserer Stärken. Auch das verstehen wir unter dem Motto “The Green Machine“.
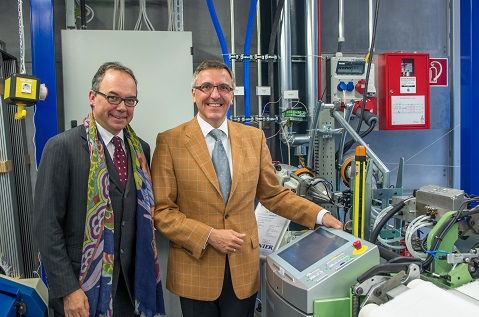
Der Wissenschaft verbunden: Peter D. Dornier (rechts) mit ITA-Chef Prof. Dr. Thomas Gries bei der Übergabe einer Luftwebmaschine A1 (Quelle: ITA)
Eine Frage zum Innovationsprozedere: Woher nehmen Sie Ihre Ideen?
Unser großes Plus ist, dass wir auf mehr Feldern unterwegs sind als alle anderen Webmaschinenhersteller. Zu unserem Kundenkreis gehören beispielsweise Drahtweber, die hochfeine Filtergewebe für Turbolader aber auch Drucker-
patronengewebe aus Metall herstellen, Carbonfaserweber, die fingerdicke Stricke auf Jacquard-Maschinen eintragen und italienische Oberbekleidungsfirmen, die mit unseren Luftwebmaschinen weiche und leichte Anzugstoffe produzieren. Etliche Impulse für neue Ideen kommen vom Transfer, also aus den Märkten bzw. direkt von unseren Kunden selbst. Wenn zum Beispiel Bekanntes auf neue Anwendungsfelder übertragen wird, ergeben sich wirklich überraschende, positive Lösungen – wie im Falle unseres massearmen Streichbaums, der speziell zum Weben von Aramidfaser für antiballistische Anwendungen entwickelt wurde: Ein italienischer Wollweber wollte wissen, ob sich die Innovation auch für Wollgewebe eigne. Genau diese Frage war es, die dazu führte, dass dieser Streichbaum mittlerweile beim Weben von Wolle auf unseren Maschinen zum Standard geworden ist. Eine andere Quelle für Innovationen ergibt sich aus der Zusammenarbeit mit einer Handvoll europäischer Markt-, Qualitäts- und Technologieführer u. a. aus dem Aerospace-Bereich.
Das Weben begleitet die Menschheit bereits seit 6.000 Jahren – steht diese textile Technologie heute vor neuen Herausforderungen und Chancen?
Absolut. Das Weben, das gerade wegen der Gleichmäßigkeit des hergestellten Materials seinen Charme hat, findet heute in einer unwahrscheinlichen Bandbreite statt: Von feinsten „ebenen“ Filtrationsgeweben für Blut oder Druckertinte bis hin zum dicken, schweren 3D-Mehrlagengewebe als Verstärkung von Transportbändern. Selbst der Internet-Riese Google beschäftigt sich neuerdings damit und hat zusammen mit dem Bekleidungshersteller Levi’s das Label „Google-Jacquard“ begründet. Ziel dabei ist es, Kleidungsstücke in Eingabeinstrumente für Smartphones und andere Mobilgeräte zu verwandeln.
Joseph-Marie Jacquard hat bekanntlich an Webstühlen für abgepasste Muster die Züge durch Lochkarten ersetzt und damit schon 1805 die erste digital gesteuerte Maschine erfunden. Ein Gewebe ist darüber hinaus aber immer „per se“ digital, der Schuss verläuft entweder über oder unter dem Kettfaden. Das heißt: Wir haben in der Weberei die einzige wirklich real-digitale Produktion, alle anderen Maschinen produzieren analoge Strukturen, auch die digital gesteuerten. Wir stehen aktuell am Beginn einer neuen Entwicklung, bei dem Gewebe nicht nur zwei- sondern auch dreidimensional strukturiert und mit reproduzierbarer, sozusagen „digitaler Qualität“ herstellen können. Das Weben als in sich digitaler Prozess hat ein enormes Potenzial, bei dem wir erst langsam erahnen, was die Zukunft – besonders für die Großserie – bringen könnte.
Was zeichnet sich ab?
Wir werden in der Zukunft mit Sicherheit noch mehr Metalle als bisher durch Kunststoffe ersetzen bzw. Metalle oder Keramiken durch textile Verstärkung noch leistungsfähiger machen können. Wenn wir mobiler werden wollen, dabei CO2-sparender, leichter und effizienter, kommen wir um Carbon-, Glas- oder Aramidfaser-Verbundwerkstoffe nicht herum. Aber auch Thermoplaste wie PA, PP und HT-Polyester werden eine – besonders mengenmäßig – wichtige Rolle spielen. Das, was ein Faserkunststoff zum Beispiel in punkto mehr Sicherheit bieten kann, wird heute bei Serienfahrzeugen nicht mal ansatzweise ausgenutzt.
Das metallische Zeitalter in der Luft- und Raumfahrt ist bereits am Auslaufen und wird auch aufgrund der CO2-Problematik in der Rückschau ein Intermezzo sein. Mein Großvater hat 1916 parallel zu Hugo Junkers sein erstes Ganzmetallflugzeug aus Aluminium zum Fliegen gebracht – letzteres blieb auf diesem Einsatzgebiet nur 80 Jahre lang das Material der Wahl. Moderne Flugzeuge bestehen schon zur Hälfte ihres Gewichts aus Textilverbundmaterialien; beim Airbus A350 sind es über 50, beim Eurofighter sogar 82 Prozent, auch wenn dort heute noch mehrheitlich textile Gelege verwendet werden.
Was ich sagen will: Gerade Gewebe werden in Zukunft verstärkt für den industriellen Bedarf benötigt werden. Ein gewebtes Großserien-Teil ist digital und wird in einem robusten Produktionsprozess absolut reproduzierbar hergestellt. Nur ein Vergleich mit Blick auf andere Textiltechnologien: Beim Weben von automobilen Airbags, also im Bereich sicherheitskritischer Bauteile, betreut heute ein einziger Techniker 40 DORNIER Webmaschinen. Bei einer großen Gelegeanlage eines Fahrzeugherstellers für Strukturbauteile aus Carbon ist es eher umgekehrt. Das Beispiel zeigt, was der Webprozess an global dislozierbarer, industrieller Effizienz bieten kann. Die weltweit führenden Airbag- oder Reifenhersteller profitieren bereits jeden Tag davon, während große Teile der Metallindustrie noch kaum wissen, was auf sie zukommt.
All das zeigt: Textil kommt wieder, aber in anderer als in der gewohnten Form, also im Flugzeug, im Auto, in Windrotoren oder auch als Obermaterial in Schuhen für Fußballprofis. Gewebte Textilien, deren Standards und Qualitäten überall auf der Welt praktisch gleich erzeugt werden können, werden dabei immer unverzichtbarer.
Sie haben zu einigen Textilforschungsinstituten langjährige Kontakte?
Mit Instituten wie dem TITV Greiz, die Grundlagen für Smart Textiles schaffen, kooperieren wir seit langem, um zum Beispiel elektrische oder schaltungstechnische Funktionen in die Jacquard-Technologie zu verankern. 3D-Strukturen mit dieser Technik herzustellen, ist für mich ein hoch spannendes Thema. Auch haben wir mit dem Institut für Textiltechnik (ITA) an der RWTH Aachen und dem Institut für Textilmaschinen und Textile Hochleistungswerkstofftechnik (ITM) an der TU Dresden strategische Partnerschaften. Um beispielsweise in Aachen die Ausbildung künftiger Textiltechniker und laufende Forschungen zu unterstützen, hat die Lindauer DORNIER GmbH erst kürzlich eine hochmoderne Luftwebmaschine vom Typ A1 gesponsert. Doch die Zusammenarbeit ist keine Einbahnstraße: Das ITA kann mit der hocheffektiven Maschine zum Beispiel die Informatisierung der Fertigungstechnik als Teilthema von Industrie 4.0 noch besser bedienen, während wir für uns bereits zwei ITA-Doktoranden gewinnen konnten.
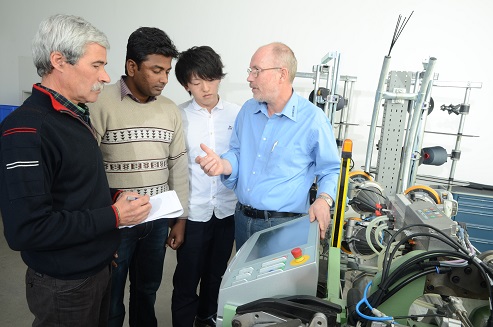
Fotoshooting DSC_5618: Kundenschulung vor Ort: Oft werden 40 Webmaschinen nur von einem Mitarbeiter betreut
Ihr Unternehmen ist weltbekannt. Gibt es für Sie eigentlich noch neue Märkte?
Geographisch betrachtet eher neue, alte Märkte, wenn ich Richtung Russland und Iran blicke. Beide Länder haben einen Investitionsrückstau von über 30 Jahren und sie wollen deutsche Technik, weil „Made in Germany“ für Effizienz, Zuverlässigkeit und lange Lebensdauer steht. Im Iran beispielsweise laufen heute noch rund 5.000 DORNIER-Webmaschinen aus den Siebzigern. Seither ist dort in unserem Metier nicht mehr viel erneuert worden. Oder nehmen Sie Russland und Indien: Beide Länder setzen beim Infrastrukturausbau zunehmend auf technische Textilien – und haben zum Teil ganz clevere Einfälle.
Zum Beispiel?
Ein großes russisches Unternehmen hat ein z. B. auch für Kanada interessantes Weltpatent auf die Herstellung von riesigen Satteltaschen, mit denen Gas-Pipelines im heute zunehmend morastigen Permafrostboden beschwert und so verankert werden können. Diese mit Erdaushub oder Steinen gefüllten Riesenbeutel bestehen aus HT-Polyestergewebe, das auf unseren Maschinen hergestellt wird.
Diesen Beitrag, eine nachrichtliche Zusammenfassung, Kurzbiografie und Unternehmensinformation mit weiteren Hintergrundinformationen im Pressedownload
Abdruck gegen Belegexemplar/Link und Quellenangabe „Umweltdienstleister“ honorarfrei.