Gesetzliche Regelungen und Einsparungen im Gesundheitswesen sorgen dafür, dass das Thema Kostendruck auch in der Pharmaindustrie eine zunehmend große Rolle spielt. Für Unternehmen rückt deshalb die Optimierung der eigenen Supply Chain immer stärker in den Fokus – von der Beschaffung über die Herstellung bis hin zur Distribution der sensiblen Produkte. In diesem Zusammenhang bieten automatisierte Logistiksysteme in der Pharmabranche viele Vorteile: von der Anpassung der Materialflussprozesse und einer Effizienzsteigerung bei der Produktion bis hin zu daraus resultierenden Kosteneinsparungen und einer Fehlerreduzierung. Die Voraussetzungen dafür: höchste Zuverlässigkeit und Genauigkeit der Logistikanlagen. Nur wenn die Intralogistiksysteme die ihnen zugeteilten Aufgaben sicher erfüllen, profitieren Unternehmen auch langfristig von einer Automatisierung. Im Fokus stehen vor allem die hohen Sicherheits- und Hygienevorschriften sowie die einzuhaltenden Qualitätsstandards. Wie diese Herausforderungen gemeistert werden können, weiß Egemin Automation.
Eins ist in der Pharmalogistik in jedem Fall sicher: Der Trend geht hin zur Automatisierung von Produktions- und Distributionsprozessen, und das nicht ohne Grund. 365 Tage im Jahr und 24 Stunden am Tag erfüllen automatisierte Lagersysteme ihre Aufgaben zuverlässig und genau – vorausgesetzt, vor der Integration stand eine nachhaltige und umfassende Analyse der Gegebenheiten, der Anforderungen und der Zielsetzung der Automatisierung durch einen Spezialisten. „Die zentrale Herausforderung besteht nämlich darin, die Intralogistiksysteme so in den Materialfluss zu integrieren, dass sie zu hundert Prozent valide, wiederholbar und kontinuierlich die Prozesse des Unternehmens abbilden und dokumentieren“, erklärt Stephan Vennemann, Geschäftsführer der Egemin GmbH in Deutschland. „Gerade in der Pharmaproduktion gilt: die richtige Ware zur richtigen Zeit in der richtigen Menge am richtigen Ort. Denn der Transport oder die Zusammenstellung falscher Stoffe kann nicht nur die Medikamentenproduktion erheblich beeinträchtigen, sondern im schlimmsten Fall auch weitreichende Folgen nach sich ziehen.“
Analyse, Konzepterstellung, Planung
Vor der Integration automatisierter Lagertechnik steht die Analyse der aktuellen und zukünftigen Geschäftsprozesse: Handelt es sich um ein Distributionslager oder die Produktionslogistik? Wie sind die Verteilprozesse organisiert? Welche Stoffe werden gelagert? Gibt es unterschiedliche Temperatur- oder Gefahrstoffbereiche? „Es ist essentiell, die Analyseergebnisse in einem Konzept festzuhalten“, betont Stephan Vennemann. „Denn diese dienen als Grundlage für die anschließende Simulation der Materialflüsse.“ Sie ist gerade im Pharmabereich unbedingt notwendig. Die Simulation überprüft praxisnah und auf Basis des Originallayouts die Planung der Materialflüsse sowie alle Transportbewegungen im Lager oder in der Produktion auf ihre Effektivität. „Die Vorgaben des Kunden dienen als Grundlage, um beispielsweise die Anzahl der fahrerlosen Transportfahrzeuge (FTF) zu ermitteln und so die Produktionskapazitäten sicherzustellen“, erläutert Vennemann. Diese bieten vor allem in pharmazeutischen Umgebungen entscheidende Vorteile, da sie in der Lage sind, aktiv Aufgaben in der Produktion zu übernehmen: Sie transportieren die verschiedenen Stoffe zu den Fertigungsmaschinen und stellen die fertigen Waren selbstständig zur Abholung bereit. Mit dem Einsatz von FTF können nicht nur Mensch und Maschine reibungslos zusammenarbeiten, auch Fahr- und Laufwege sind frei passierbar und die Abläufe in der Produktion somit flüssig. „Im Rahmen der Integration eines fahrerlosen Transportsystems (FTS) gehören zur Simulation auch die Ermittlung der Fahrgeschwindigkeit der Fahrzeuge und die Festlegung der Routen von Produktionsmaschine zu Produktionsmaschine oder vom Lager zum Warenausgang“, erklärt Vennemann. „In dem Zusammenhang lässt sich testen, wie das Logistiksystem auf unterschiedliche Vorgaben reagiert.“ Kommen mehrere simulierte Modelle zu demselben Ergebnis, kann davon ausgegangen werden, dass es zuverlässig seine Aufgaben erfüllt und unter Berücksichtigung der Produktions- und Logistikprozesse die geplante Leistung erbringt. Auf Grundlage einer Simulation lassen sich auch zu einem späteren Zeitpunkt noch weitere Anpassungen vornehmen. Somit können zukünftige Prozesse und deren Auswirkungen auf das Gesamtsystem schon vorab betrachtet und bewertet werden. Darüber hinaus sind FTS im Vergleich zur festinstallierten Fördertechnik so flexibel, dass eine Umstellung der Produktion oder ein Wechsel in den Rezepturen in nur wenigen Schritten einfach durchzuführen sind.
Temperaturführung und Gefahrgut
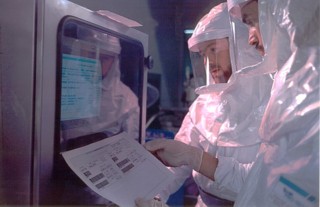
(Bild: Egemin)
Nicht nur die exakte Planung des Materialflusses ist eine Herausforderung in der Pharmalogistik, auch das oftmals sehr breite Artikelspektrum stellt einen kritischen Parameter für die Logistikanlagen dar. So gilt es beispielsweise, verschiedene Temperaturbereiche logistisch zu erfassen oder Zusammenlagerungsverbote mit Gefahrgut zu berücksichtigen. Eine Simulation im Vorfeld bietet in diesem Fall eine gute Lösung, um die zuverlässige Konsolidierung der Stoffe aus den verschiedenen Bereichen zu gewährleisten. Die Planung der Materialflüsse kann dann beispielsweise anhand von Rezepturen erfolgen. Dafür muss wiederum eine fehlerfreie Schnittstellenkommunikation zwischen der Lagerverwaltungssoftware, der Produktion und der Rezepturdatenbank gewährleistet sein. Eine besondere Rolle spielen die Schnittstellen zwischen den einzelnen Softwaremodulen, die sich gegenseitig Aufträge erteilen und Abschlussmeldungen geben. Je nach Produktionsart müssen sehr viele verschiedene Anlagen und Prozesskomponenten miteinander kommunizieren. Die Simulation gibt in diesem Fall schnell Aufschluss, wo potenzielle Kapazitätsengpässe bestehen oder nicht durchgängige Prozesse stattfinden. „Gerade in der Pharmaproduktion greifen wir als Systemintegratoren sehr tief in den Fertigungsprozess ein, weil wir die genauen Abläufe bei der Produktion kennen und die Kommunikation zwischen den einzelnen Anlagen analysieren müssen“, erklärt Stephan Vennemann weiter. „Das ist aber notwendig, weil nur so die Durchgängigkeit und Prozesssicherheit der Logistikanlagen gewährleistet werden kann.“
Hygienestandards, Sicherheitsmaßnahmen und gesetzliche Vorgaben
Damit automatisierte Logistiksysteme die Materialflüsse in der Pharmaproduktion oder -distribution genau abbilden, ist es wichtig, diese zu validieren. „Das Thema ist bei Egemin entscheidend. Deshalb steht im Unternehmen eine eigene Division zur Verfügung, die sich ausschließlich mit der Validierung im Life-Science-Bereich beschäftigt“, berichtet Stephan Vennemann. Validierung heißt: Die strengen rechtlichen Vorgaben, die Anforderungen an Hygiene und Qualität sowie verschiedene Vorgänge zur Reinigung der Behälter zwischen den einzelnen Produktionsstufen werden im Vorfeld kritisch analysiert. Nur wenn diese Prozesse und Funktionen anhand festgelegter Standards vorab getestet und dokumentiert werden und diesen Prüfungen standhalten, ist das System valide. Das heißt, es kann gemäß den geltenden Regelungen und Standards seine Aufgaben erfüllen. Vor allem in Bezug auf die einzuhaltenden Hygienemaßnahmen bietet die Automatisierung einen entscheidenden Vorteil: Während Personal umfangreiche Schutzmaßnahmen etwa in Form von Schutzkleidung ergreifen müsste, erfüllt ein automatisches Logistiksystem – einmal validiert – die ihm zugewiesenen Aufgaben zuverlässig, kontinuierlich und selbstständig. „Hier kommt neben der Prozesssicherheit auch der Faktor Zeit mit ins Spiel“, weiß Vennemann. „Schutzmaßnahmen, die das Personal ergreifen muss, dauern sehr lange. Ist ein System einmal validiert, reagiert es mit den hinterlegten Prozeduren automatisch auf Abweichungen – und das 24 Stunden am Tag und 365 Tage im Jahr.“
Transportsicherheit im Fokus
Die Transportsicherheit und der sensible Umgang mit den Pharmaprodukten sind eine weitere Herausforderung vor der Einführung automatisierter Lagertechnik. Nicht immer handelt es sich bei pharmazeutischen Artikeln um Feststoffe. Entsprechend sind die Transportmittel anzupassen. Für Flüssigkeiten sind je nach Bedarf des Kunden spezielle Sonderbehältnisse nötig, damit die auch über die automatisierte Fördertechnik transportiert oder von den FTF aufgenommen werden können. Bei der Planung des Materialflusses ist darüber hinaus zu beachten, welche Erschütterungstoleranzen für die einzelnen Stoffe zulässig sind. Entsprechend ist dann die Fahrgeschwindigkeit oder die Bodenbeschaffenheit zu berücksichtigen oder anzupassen. „Von Gestellen und normalen Paletten bis hin zu Behältnissen, die Gefahrgut befördern dürfen: Für uns als Systemintegrator für die Pharmalogistik ist es notwendig, flexibel auf die Anforderungen eingehen zu können und bereits vor der Automatisierung verschiedene Szenarien durchzuspielen“, betont Stephan Vennemann von Egemin. „Nur so findet man die beste, sicherste und nachhaltigste Lösung.“
Egemin
Messestand: Halle 17, Stand E72/1